
There are a number of strategic steps you can take to enhance your supply chain with greater flexibility and agility. When it comes to your material handling equipment needs, the best step you can take is implementing a forklift fleet and operator management system. When utilized effectively, the right system can guide and inform an approach that increases flexibility and agility while helping maintain lean principles and identifying opportunities for increased efficiencies.
Following are two important ways in which a good forklift fleet and operator management system can create a more resilient supply chain with greater flexibility and agility.
It’s safe to say that last year derailed most businesses’ forecasting and projecting models. At this point, it remains difficult to comprehend how businesses, supply chains and customer behavior have been permanently changed. It can be especially challenging as you try to determine the differences between durable demand, new peaks or permanent changes in demand. This makes data more important than ever as you look to gain insight and better understand your operation and keep pace with customer demands and expectations.
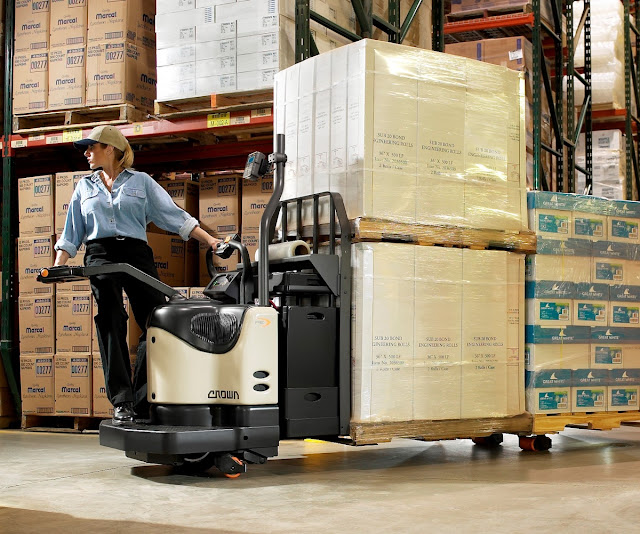
Given the prominent role that forklifts play in the supply chain, there is a wealth of data that can be gathered through forklift fleet and operator management systems, including data on operator performance, product movement and how, when and where your forklift fleet is being used. Knowing the performance of your fleet and operators is especially vital as you deal with demand fluctuations, supply chain disruptions and evolving forecast models.
And it’s not enough to just gather the data. You need to have a plan to institute accountability and action. To realize success, you need to have in place the processes, resources, support (internal and external) and commitment to make decisions and take action based on what the data reveals. You can consult with your provider to understand what can be captured, then analyze what is significant and how you can best act on it.
Another way an effective forklift fleet and operator management system can help you better prepare operations for unexpected shortages and delays, as well as shifting consumer expectations, is helping you determine the right mix of lift trucks for your operations and objectives. This is more than right-sizing. While ensuring your fleet is being utilized by the right operators, at the right times, in the right locations is important, it is equally important that you have the right trucks and technology comprising your fleet to effectively and efficiently get your products out the door.
For instance, as many retail and grocery companies are being challenged to move as much product as possible, as quickly as possible, they are also being pressured to maintain facility footprints by building up and not out to increase storage density within existing space. To go higher in the warehouse, you need a forklift that can optimize warehouse slotting by placing heavier loads at higher heights with faster speeds, while also maintaining safety standards with greater operator control and visibility.
Additionally, as operations seek ways to quickly accelerate productivity to meet fast-changing customer demand while addressing the new paradigm of the socially-distanced warehouse worker, interest in automation has grown dramatically. A flexible automation solution gaining attention is dual mode technology that enables forklifts to switch between manual and automated operations, depending on the needs of the facility. This enables warehouses to take an incremental approach to deploying automation, with minimal supporting infrastructure and with or without a warehouse management system.
The data gathered from your forklift fleet and operator management system can help you identify those tasks and equipment that are ideal for automation and develop a clear path for tangible ROI. Having the right data enables you to quickly and strategically grow and evolve your automation efforts, adding diversity and flexibility to your forklift fleet.
There has never been a time of more uncertainty and unpredictable changes within the supply chain. Unprecedented demands and changes in consumer behavior are forcing many companies to rethink their operations and more succinctly plan for the unexpected. Implementing a forklift fleet and operator management system and acting on the data it gathers can make powerful progress toward building and maintaining more flexibility and agility in your supply chain.
Source: https://blog.crown.com/
Comments
Post a Comment